Mullite Brick
Mullite Brick – High-Performance Refractory Solution for Industrial Furnaces
Manufacturer & Global Supplier of Fused and Sintered Mullite Refractory Bricks
Mullite bricks are high-alumina refractory materials with mullite (3Al₂O₃·2SiO₂) as the primary crystalline phase, typically containing 65% to 75% Al₂O₃. Based on the manufacturing process, mullite bricks are mainly classified into sintered mullite bricks and fused mullite bricks.
Characters of Mullite Bricks:
• 🔥High Working Temperature:Operating reliably at up to 1700°C, suitable for extreme industrial furnaces.
• ⚡Superior Thermal Shock Resistance:Excellent performance in rapid temperature cycling conditions.
•❄️ Low Thermal Conductivity:Improves energy efficiency and minimizes heat loss.
• 🛡️Corrosion & Erosion Resistance:Resists attack from slags, alkalis, and flue gases.
• 🧱Custom Shapes & Sizes Available:Tailored to meet your furnace design specifications.
Typical Applications of Mullite Bricks:
•🏭Steel Industry: Furnace walls, roofs, burner blocks
•🫙Glass Industry: Regenerators, forehearths
•🏗️Cement Industry: Kiln linings and transition zones
•⚗️Petrochemical Plants: Reformer linings, cracking furnaces
•🔥Incinerators & Boilers: High-temperature zones requiring alkali resistance
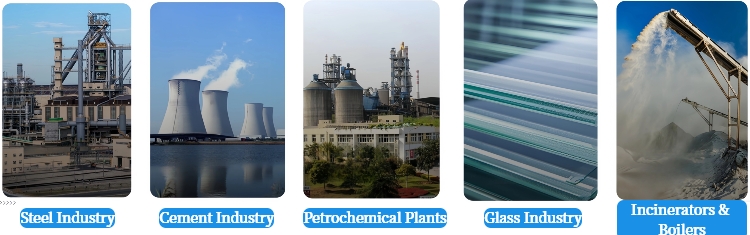
Parameters of Mullite Bricks:
Item | MLZ-60 |
MLZ-65 |
MLZ-70 |
MLZ-75 |
Al₂O₃(%)≥ |
60 | 65 | 70 | 75 |
SiO₂(%)≤ |
35 | 33 | 26 | 24 |
Fe₂O₃(%)≤ |
1.0 | 1.0 | 0.6 | 0.4 |
Apparent porosity(%)≤ |
17 | 17 | 17 | 18 |
Bulk density(g/cm³)≥ |
2.55 | 2.55 | 2.55 | 2.55 |
Cold crushing strength(MPa)≥ |
60 | 60 | 80 | 80 |
Refractoriness under load, ℃(0.2MPa,0.6%)≥ |
1580 | 1600 | 1600 | 1650 |
Permanent Linear Change On Reheating,%(1500℃*2h) |
0~+0.4 |
0~+0.4 |
0~+0.4 |
0~+0.4 |
Thermal Shock Resistances 100℃ water cycles≥ |
18 | 18 | 18 | 18 |
Thermal Conductivity (W/MK) 1000℃ |
1.74 | 1.84 | 1.95 | 1.95 |
Q:What is the maximum working temperature of mullite refractory bricks?
A:Mullite bricks can typically withstand temperatures up to 1700°C (3092°F), making them ideal for high-temperature industrial furnaces and kilns.
Q:What is the difference between fused mullite and sintered mullite bricks?
A:•Fused mullite bricks are made by melting raw materials in an electric arc furnace and then cooling them rapidly, resulting in low porosity and high strength.
•Sintered mullite bricks are produced by high-temperature sintering of mullite-rich materials, offering better thermal shock resistance and cost-efficiency.
Q: Are mullite bricks resistant to thermal shock?
A:Yes. Mullite bricks are known for their excellent thermal shock resistance, enduring repeated heating and rapid cooling cycles without cracking or spalling.
Q: What sizes and shapes are available for mullite bricks?
A:We offer standard sizes (230×114×65mm) and customized shapes such as arch bricks, keys, wedges, or according to your furnace design or OEM drawing.
Q: Can you supply mullite bricks with customized physical properties?
A:Absolutely. We can adjust Al₂O₃ content, density, porosity, and strength to suit specific project needs, whether you need alkali resistance, abrasion resistance, or lightweight insulation.
Q: What is your minimum order quantity (MOQ) for mullite bricks?
A:Our typical MOQ is 5 tons, but we can support smaller trial orders or container loads depending on your project.
Q: Do you provide technical support or installation advice?
A:Yes. We offer full technical consultation, including material selection, lining design, and construction guidance to ensure optimal performance.
Q:Are your mullite bricks suitable for export markets?
A:Yes. Our mullite bricks are widely exported to Southeast Asia, Europe, the Middle East, Africa, and other regions. We offer export-standard packaging, fast delivery, and customs clearance support.