Magnesium Iron Spinel Brick
Magnesia Hercynite Bricks - Superior Thermal Shock Resistance and Chemical Stability for Demanding Applications
Magnesia Hercynite Bricks are advanced refractory products made from high-purity magnesia (MgO) and synthetic hercynite (FeAl₂O₄) spinel. Designed for extreme working environments, these bricks offer outstanding thermal shock resistance, excellent corrosion resistance to slag and alkali vapors, and remarkable structural integrity at high temperatures.
Industry Pain Point Solutions:
1.Extended Cement Kiln Lifespan
Reduce frequent shutdowns caused by alkali corrosion in transition zones, extending campaign cycles to 12-18 months.
2.Lower Steel Ladle Maintenance Costs
High slag penetration resistance minimizes lining thickness, increasing effective molten pool capacity by 15-20%.
3.Energy Efficiency Optimization
Enhanced thermal conductivity (2.0-2.5 W/m·K) reduces fuel consumption in lime kilns, improving overall thermal efficiency by 8-12%.
Characters of Magnesia Hercynite Bricks:
•✅Excellent thermal shock resistance
•✅Strong resistance to slag and alkali corrosion
•✅High mechanical strength and structural stability
•✅Reduced shrinkage and deformation under high temperatures
•✅Long service life in harsh industrial environments
Main Applications of Magnesia Hercynite Bricks
•Cement Industry: Transition zones, burning zones, and preheater linings
•Steel Industry: Secondary metallurgy units, RH degassers
•Non-Ferrous Metallurgy: Smelting furnaces for copper and nickel
•Waste Incineration: Combustion chambers and rotary kilns
•Chemical Plants: Reactor linings exposed to aggressive gases
Item |
MLZ-01 |
MLZ-02 |
MgO (%) ≥ |
85 | 88 |
Fe₂O₃ (%) |
5~7.5 | 5~6 |
SiO₂ (%) ≤ |
2.0 | 1.5 |
Al₂O₃ (%) |
3.0~5.0 | 4.0~7.0 |
Apparent Porosity (%) ≤ |
17 | 16 |
Bulk Density (g/cm³) ≥ |
3.0 | 2.9 |
Cold Crushing Strength (Mpa) ≥ |
45 | 55 |
Refractoriness Under Load (0.2MPa×0.6%) °C ≥ |
1600 | 1650 |
Thermal Shock Resistance (1100°C, water cooling) cycle ≥ |
6 | 8 |
Thermal Conductivity (350°C ± 25°C) W/(m·K) ≤ |
2.6 | 2.6 |
Thermal Expansion % (1400℃) ≤ |
1.6 | 1.7 |
FAQ:
Q: What advantages do Magnesia Hercynite Bricks offer compared to traditional magnesia bricks?
A: They provide superior thermal shock resistance, lower thermal conductivity, better structural integrity, and extended service life, especially in rotary kilns and aggressive furnace environments.
Q: Where are Magnesia Hercynite Bricks commonly used?
A: They are widely used in cement kilns (transition and burning zones), secondary metallurgy units, waste incinerators, and non-ferrous metal smelting furnaces.
Q: What is the maximum service temperature for Magnesia Hercynite Bricks?
A: They can typically withstand temperatures up to 1700°C, maintaining excellent mechanical and chemical stability.
Q: Can you supply customized sizes and shapes?
A: Yes, we offer customization services for different sizes, shapes, and compositions based on your specific operating conditions and project requirements.
Q: How is the thermal shock resistance of Magnesia Hercynite Bricks?
A: Outstanding — they can endure repeated thermal cycling at high temperatures without cracking or significant degradation.
Q: Do you provide technical support for installation and maintenance?
A: Yes, we provide full technical support, including material selection advice, lining design recommendations, and installation guidelines.
Q: What is the typical delivery time for Magnesia Hercynite Bricks?
A: Standard production and delivery time is about 15–30 days, depending on order volume and customization needs.
Q: How do you ensure product quality?
A: We implement strict quality control during raw material selection, production, and final inspection. Third-party testing and certifications are also available upon request.

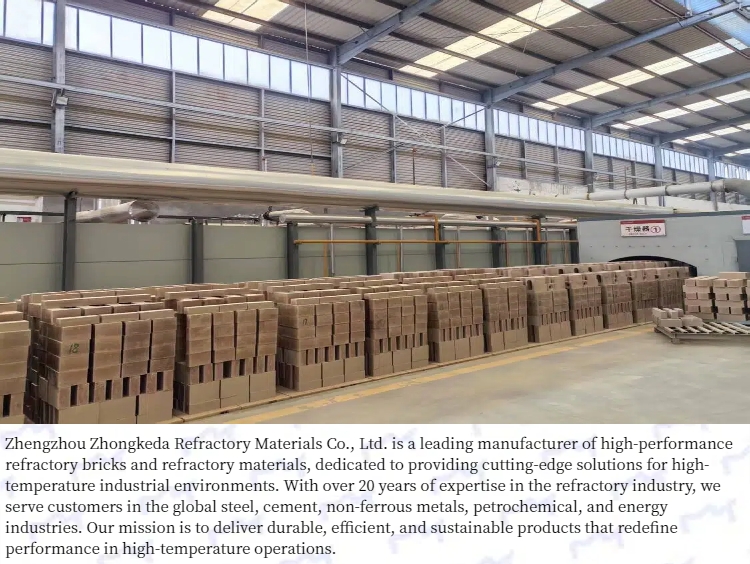
