Magnesia Carbon Brick
Magnesia Carbon Bricks - Premium Refractory Solution for High-Temperature Steelmaking Applications
Magnesia-carbon bricks are made from high-purity magnesia, carbon materials (including graphite), and tar pitch or resin through batching, hot mixing, molding, and firing at temperatures ranging from around 300℃ to over 1000℃. These bricks effectively utilize the strong slag resistance of magnesia and the high thermal conductivity and low expansion of carbon, compensating for the poor spalling resistance of magnesia. As a result, magnesia-carbon bricks feature excellent slag resistance, good slag penetration resistance, high thermal shock stability, and superior thermal conductivity.
Characters of Magnesia Carbon Bricks:
✅ High refractoriness and strength at elevated temperatures
✅ Excellent thermal shock resistance
✅ Superior resistance to chemical corrosion and slag penetration
✅ Low thermal expansion and good oxidation resistance
✅ Prolonged service life and reduced downtime
Main Application of Magnesia Carbon Bricks:
•🏭Steel Industry: BOF, EAF, ladles, converters
•🧪Non-Ferrous Industry: Copper and nickel refining furnaces
•🔥Industrial Furnaces: High-wear lining zones
•🧱Furnace Accessories: Impact pads, slag lines, working linings
Parameters of Magnesia Carbon Bricks:
Item
Apparent Porosity(%)≥
Bulk Density(g/cm³)≥
Cold Crushing Strength(MPa)≥
MT10A
80
10
4
2.9
40
6
MT10B
78
10
5
2.85
35
5
MT10C
76
10
6
2.8
30
4
MT14A
76
14
4
2.9
40
12
MT14B
76
14
5
2.82
35
8
MT14C
74
14
6
2.77
25
5
MT18A
72
18
3
2.9
40
10
MT18B
70
18
4
2.82
35
7
MT18C
70
18
5
2.77
35
4
FAQ:
Q: What are the advantages of using Magnesia Carbon Bricks in steelmaking?
A: They provide excellent thermal shock resistance, superior corrosion resistance against slag and steel, high refractoriness, and longer service life, reducing maintenance and downtime in harsh furnace environments.
Q: In which areas of steel plants are Magnesia Carbon Bricks typically used?
A: They are commonly used in basic oxygen furnaces (BOF), electric arc furnaces (EAF), steel ladles, converters, and tundishes, especially in slag lines, impact zones, and working linings.
Q: Can the chemical composition and physical properties be customized?
A: Yes, we can tailor the MgO content, graphite percentage, and other properties according to specific working conditions and customer requirements.
Q: What is the typical service life of Magnesia Carbon Bricks?
A: Service life varies based on furnace conditions, but our high-quality MgO-C bricks typically last longer due to superior wear resistance and low oxidation loss.
Q: Do you offer technical support for brick selection and installation?
A: Absolutely. Our technical team can assist you with material selection, installation recommendations, and lining design optimization to maximize furnace performance.
Q: What is your Minimum Order Quantity (MOQ)?
A: Our standard MOQ is 10 tons, but smaller trial orders can be negotiated for new clients or specific project needs.
Q: How are Magnesia Carbon Bricks packaged for shipment?
A: Bricks are packed on fumigated wooden pallets with waterproof wrapping, ensuring safe transportation to your site.
Q: Can I request a product sample for testing before placing a bulk order?
A: Yes, samples are available upon request. Shipping costs for samples are usually borne by the buyer.
Q: Do your products meet international quality standards?
A: Yes. Our Magnesia Carbon Bricks are manufactured under strict quality control systems and can be provided with ISO certification, chemical analysis reports, and third-party inspection documents if required.

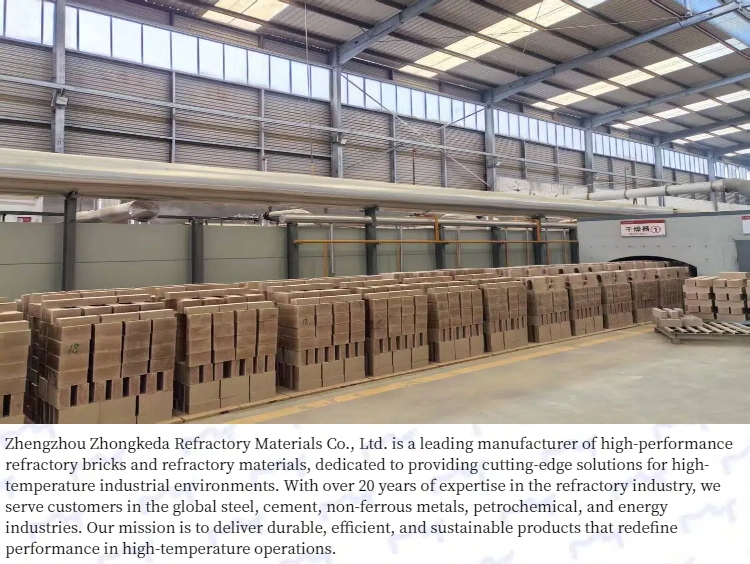

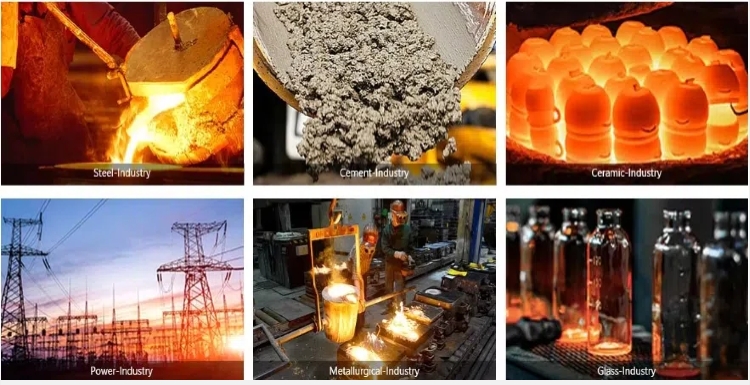

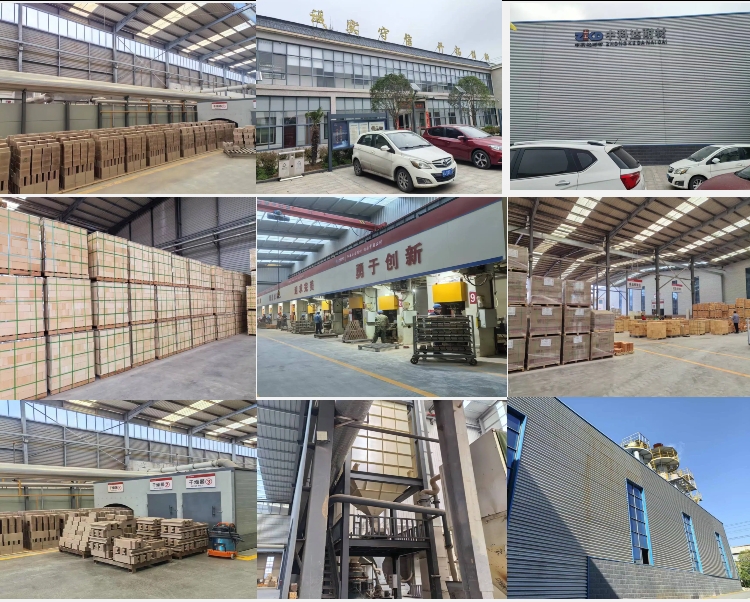